Reduce Your Feed Costs by Working to Improve Efficiencies and Effectiveness
In todays’ business environment, your cooperative faces unprecedented challenges as we work to serve our patrons. Supply chain problems, ingredient and materials shortages, labor/staff limitations, rising costs of fuel, high cost of replacing equipment, and regulatory mandates are constant stressors on our business.
The feed supply business, like farming operations, is extremely labor and equipment-dependent. We have had issues with ingredients and essential nutritional additives arriving to feed mills on time due to trucker shortages in the past year. Products we used to order and receive in 48 hours now take as much as four weeks or more to arrive. We used to order and forget about it- the product just showed up. Today, we order and then track, follow up, and worry about when the product will arrive.
Replacement of rolling stock, milling equipment, repairs, and preventative maintenance have increased in cost 25-50% in a short two years! Labor costs to retain and attract good workers have gone up as much as 25%! Fuel is also much more expensive than a year ago. Diesel, the primary fuel used in feed delivery, is up over $1.10 a gallon in the past year and shows no sign of going down while at the same time regulatory emissions controls reduce miles per gallon.
Despite the challenges mentioned above, United Cooperative’s Feed division has continued to find efficiencies and cost containment measures. We ask our customers to help us in reducing costs by doing the following:
- Give the feed mill extra lead time on orders. The same-day order and delivery days are gone, and orders must be scheduled days in advance to maximize efficiency. Staging maximizes mill flow and truck coordination allowing us to schedule loads and coordinate trucks for maximum effectiveness. Extra lead time also allows us to have the required ingredients in stock to make your feed.
- Consider larger feed bins and coordination of multiple mixes on same truck delivery. We have trucks with 4-7 compartments that allow us to deliver numerous mixes to your farm. Combining multiple mixes saves on trips, reducing the cost of fuel and time on the road. A single delivery of 23+ tons of feed is much more efficient and lower in cost than two 11-12 tons deliveries.
- Consider working with the mill on a keep fill program, which allows our mill to ensure you do not run out of feed while leveling out work schedules throughout the week.
- Evaluate your on-farm storage bins. Are your bins large enough to contain full loads of feed? If not, contact us about programs to assist you in the correct sizing for your feed storage. We have programs for lease-to-own bins that reduce cash flow and may allow you to maximize delivery discounts and minimize freight costs.
Please help us reduce your feed costs by working to improve efficiencies and effectiveness.
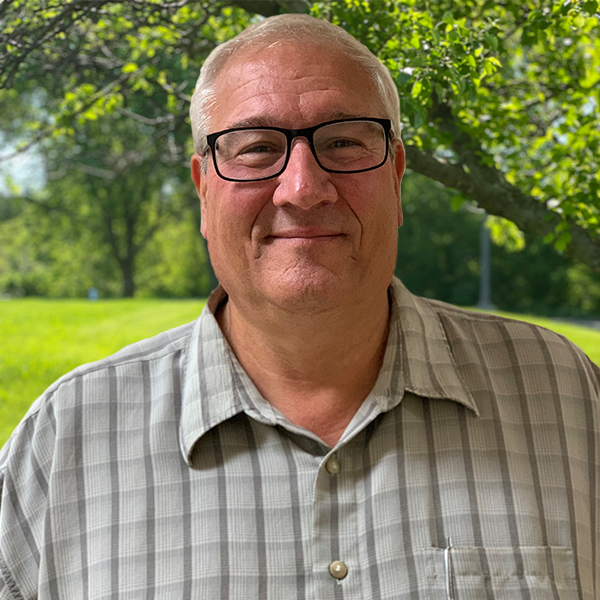
Dan Jensema
Feed Marketing Manager